Changing consumer habits are driving demand for a new type of logistics space – the e-fulfilment centre. Coupled with the rise in automation and the diversity of processes taking place in a modern logistics hub, these centres are requiring more soft labour skills rather than the traditional muscle of the warehouse space.
“Our clients are waking up to the fact that they cannot treat labour as a commodity anymore” – Stephen Fleetwood, CBRE
While the demand for logistics space is being led by the consumer, the shortage of labour is the forming factor on the supply side, especially in the markets of the Czech Republic, Germany and Benelux, identifies the Prologis report, Top Solutions to Source, Train & Retain Labour in Logistics Facilities.
CBRE cites the Czech Republic as having just seven unemployed people per job vacancy in transportation and storage. Stephen Fleetwood, Head of Location Advisory, EMEA, CBRE, said at the MIPIM session on Labour Trends Impacting the Logistics Real Estate Market: “Our clients are waking up to the fact that they cannot treat labour as a commodity anymore.”
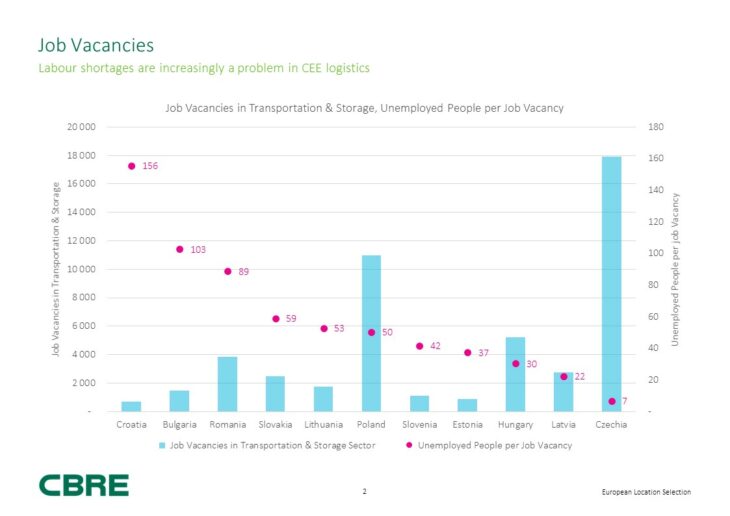
Source: CBRE
The number of jobs created in the logistics sector has risen year-on-year across the European Union to reach a cumulative figure of over 884,000 in 2019, according to fDi Intelligence.
Labour accounts for around 25-30% of supply chain costs, estimates Prologis, and the shortage of labour is driving both the developer and the occupier to look at ways of improving the working environment and conditions, as well as the career opportunities for employees.
Source: fDi Intelligence“Automation is expensive, and it’s limited. Machines can’t select screwdrivers and washing machines; humans can” – Stephen Fleetwood, CBRE
“If anything, labour shortages are becoming even more acute as economies have grown and there are more job opportunities around,” added Fleetwood. “And let’s face it, the perception is that a warehouse isn’t the most fun place to work, and we need to change that perception!
“Naturally, everyone then thinks, just automate. The problem with automation is that it’s expensive, and it’s limited. Machines can’t select screwdrivers and washing machines; humans can,” said Fleetwood. “It’s about finding the tipping point between automation and labour.”
Philippe Raffner, Director of Group Client Solutions, the Adecco Group, said that two or three years ago, the industry was expecting automation to bring in huge changes. “Some parts of the logistics are now automated, such as drones carrying out the inventory or robots helping workers with heavy work, but the movement is not so strong or so quick as we had originally thought,” he added.
Logistics: surge of investment & high occupancy
Across Europe, ecommerce sales – the driver behind the demand for logistics space – are expected to grow 8.5% a year till 2023, with fashion being the market’s largest segment.
The UK is Europe’s most developed ecommerce market, with online retailing accounting for about 60% of warehouse demand, up from a third ten years ago, says CBRE.
Across the Atlantic, the Financial Times described the US logistics market at the end of last year as “a warehouse gold rush fuelled by ecommerce”.
“Many investors are looking at moving up the risk curve as they cannot get the product” – Alison Abbey, Eastdil Secured
At the MIPIM session Logistics: Navigating the Perfect Storm, Alison Abbey, Director, Eastdil Secured, described the buoyancy of the logistics investment market in Europe as having “no abatement in the weight of capital seeking to go into the sector, with many investors looking at moving up the risk curve as they cannot get the product.”
“The base line is to get the right location, ensure your product is flexible and to grow your income by actively managing your asset through rental growth” – Thomas Karmann, AXA Investment Managers – Real Estate
On the same panel, Thomas Karmann, Head of Logistics, AXA Investment Managers – Real Estate, added: “Over the last couple of years, you could have bought a portfolio, done nothing with it and today it would be worth more. Now the base line is to get the right location, ensure your product is flexible and to grow your income by actively managing your asset through rental growth, as high occupancy rates mean that you cannot achieve this through increasing occupancy.”
The Renault Group launches programme to attract the younger generation
Robert Wittenberg, Head of Corporate Real Estate Offices & Logistics, the Renault Group, who was on the panel for the MIPIM session on the logistics labour force, said that a more skilled workforce was now required. “The workforce needs to be capable of managing IT issues, and they have to have the cost awareness, as well as the skills to manage robots and automation,” he said.
To have access to a quality workforce, Renault’s new warehouses are focused on logistic hubs and have a maximum size of 30,000-40,000 sq m.
Labour scarcity is leading Prologis customers to consolidate operations – in particular in and near major population centres
This reflects the trend highlighted in the Prologis survey of 206 warehouse users which cites that labour scarcity is leading their customers to consolidate operations – in particular in and near major population centres – rather than to relocate or decentralise.
The Renault Group, which employs around 2,500 people in their logistics warehouses in Europe, has launched a ‘staff leasing’ programme to attract a younger generation of employee.
The ‘staff leasing’ contract is permanent, and employees work in different warehouses on different tasks, in proximity to where they live. As part of the programme, they also undertake off-site training; this is mainly in soft skills, given that the hard skills are learnt on the job.
Zalando believes in ‘connected retail’
With the ‘last mile’ of the ecommerce supply chain a current hot topic, the logistics sector is looking at ways of integrating logistics into urban mixed-use schemes. (Noise disturbance in residential districts can be an issue, the panel pointed out.)
Reducing a building’s footprint – especially relevant in high-priced urban areas – is also now viable through the arrival of vertical warehousing, made possible by the rise of automation.
However, last-mile logistics is still only a small share of the market. Instead, Raimund Paetzmann, VP Corporate Real Estate, Zalando SE, Europe’s leading online fashion platform, believes in ‘connected retail’. This is about connecting physical retail partners to form a Zalando ‘city logistics’ network.
“If the item is available in the Adidas brand store in Berlin, for example, we send it directly to the customer by courier from the store” – Raimund Paetzmann, Zalando
If a customer in Berlin orders an Adidas product online from Zalando, the item would normally be delivered from one of the six EU Zalando fulfilment centres, said Paetzmann.
“With our ‘connected retail’ network, we will check to see if the item is available in the Adidas brand store in Berlin, and if it is, we send it directly to the customer by courier from the store.”
The world’s first WELL CertifiedÔ Gold logistics project
At the MIPIM session on labour trends in logistics, Ben Bannatyne, President Europe, Prologis, highlighted the four key areas identified by Prologis to help real estate owners attract, train and retain logistics workforces:
- Better transport connections – bike paths, shuttle buses & mobile apps to encourage car sharing.
- High-quality amenities – quality food, indoor & outdoor social and recreational areas.
- Logistics career and community commitment
- Improvement of building characteristics.
Prologis has joined forces with the International WELL Building InstituteÔ – already known for its certification work in offices and retail – to launch a standard for logistics projects.
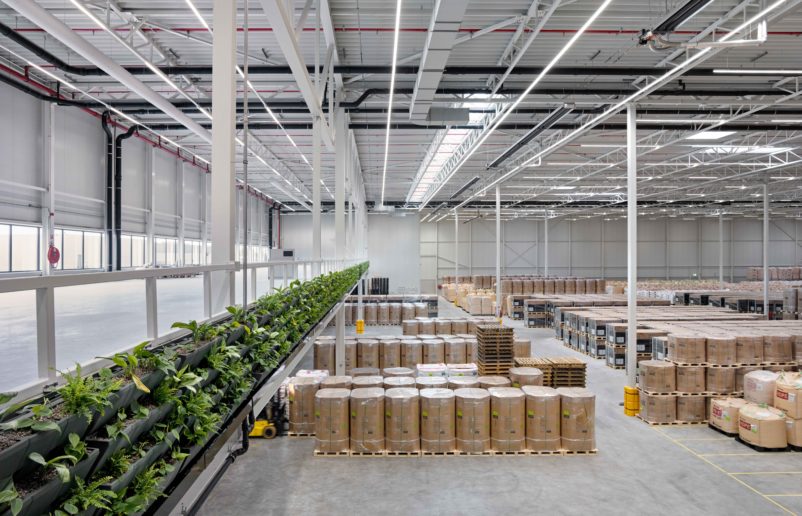
Prologis Park
This new standard focuses on seven human-oriented categories of building performance: air, water, nourishment, light, fitness, comfort and mind. “Shifting toward a more human-centric approach leads to insights that give Prologis buildings an extra competitive edge,” says the world-leading logistics developer and owner.
The world’s first logistics project to achieve the WELL CertifiedÔ Gold is Tilburg DC5 at Prologis Park Tilburg in the Netherlands. Prologis delivered the 28,000 sq m built-to-suit distribution facility, shortlisted for this year’s MIPIM Awards, to Pantos Logistics in May 2018.
Features at DC5 include air filtration, green walls, 100% wool acoustic walls, circadian lighting and water points on each floor, providing carbon-filtered water.
No longer is warehousing about a big shed surrounded by fields and with easy access to a motorway slip road; it’s about people.
Sources/credits:
- Chart showing cumulative jobs created by cross-border logistics investment in Europe 2003-2019 – fDi Intelligence, The Financial Time Group 2019.
- Chart showing job vacancies – CBRE.
- All logistics warehouse images are of Prologis Park Tilburg DC5, WELL-building facility.